
10 Fun Facts About the Sunset Park Material Recovery Facility, NYC’s State of the Art Municipal Recycling Facility

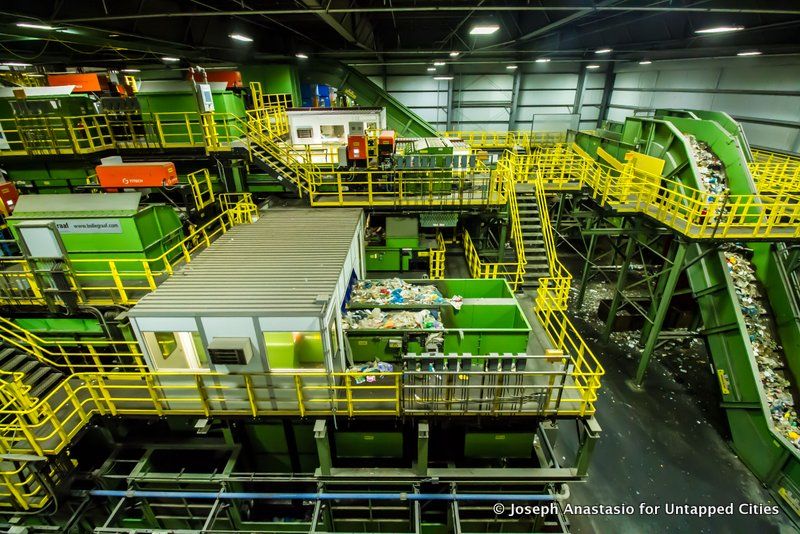
In one of our Behind the Scenes Tour series, produced in partnership with the NYCEDC, we brought Untapped Cities readers into the Sims Sunset Park Material Recovery Facility at the South Brooklyn Marine Terminal (SBMT). This state-of the-art, 11-acre recycling facility along the Sunset Park waterfront opened in December 2013, having survived the onslaught of Hurricane Sandy while under construction due to the foresight of numerous flood protection initiatives.
The Sunset Park Material Recovery Facility is the anchor to New York City’s curbside collection program, processing all plastic, metal, and glass collected by the Department of Sanitation. But the location’s technological features extend beyond just the recycling process itself – the building and site incorporate many sustainable elements.
Here are 10 fun facts we learned on our behind the scenes visit:
1. 18,000 Tons of Metal, Glass, Plastic and Paper are Received Every Month
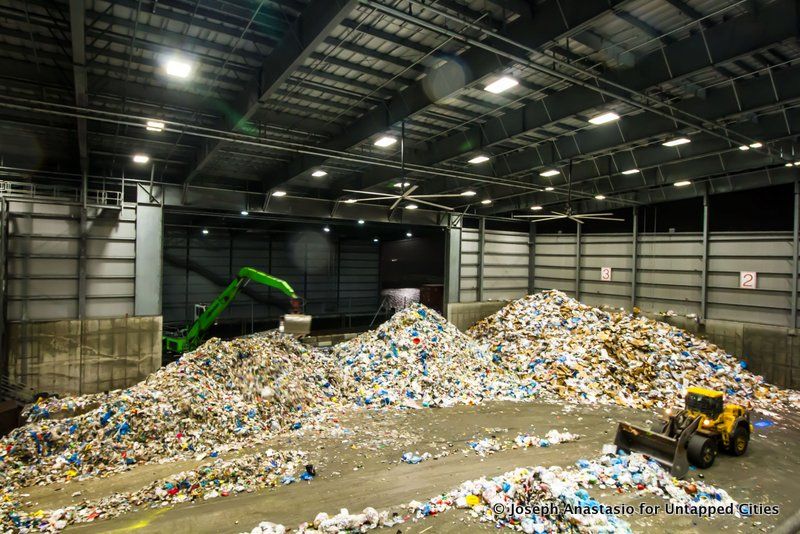
Tipping Floor at the Sunset Park Material Recovery Facility
Each month, the Sunset Park Material Recovery Facility processes 20,000 tons of the residential metal, glass and paper picked up by the New York City Department of Sanitation (commercial waste is not handled by the city). The metal, glass and plastic (referred to as MGP) arrives completely mixed together. It first enters a place known as the tipping floor, shown above, and a front-end loader pushes the recyclables onto a conveyor belt. The conveyor feeds up into a “Liberator Shredder,” a slow-speed shredder with large gaps between the teeth that is used to open up the plastic bags that the recyclables come in. The recyclables fall through along with the ripped open bags.
2. The Facility Receives 30 Tons of Plastic Bags a Day

The Sunset Park Material Recovery Facility receives 30 tons of plastic bags a day. Doing the math, this means on a 30-day month, the Sunset Park Material Recovery Facility receives 900 tons of plastic bags or 5% of its total monthly intake. Our guide, Eadaoin Quinn, Education Coordinator for Sims Municipal Recycling, tells us that while most of the products distilled from the collections are sold on the east coast and in Canada, there are no buyers for plastic bags in the United States.
3. Material Arrives and Leaves by Barge, Rail and Truck
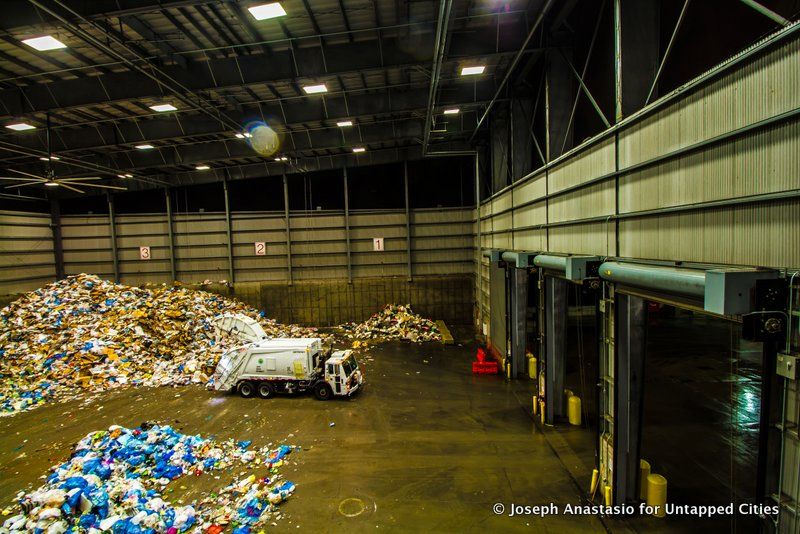
The collected materials are dropped off by both barge and truck (
about 60% by barge). Material from Queens and the Bronx mostly arrives by barge, and material from Brooklyn arrives directly by truck. Processed materials leave by truck, rail and barge float.Fun fact: All tin cans leave the facility by rail. Approximately once a week, New York New Jersey Rail picks up 2 to 4 rail cars full of cans crushed into cubes. It then pulls those cars down through Sunset Park to 65th Street Railyard, where it puts those cars onto a “carfloat” (basically, a barge with tracks on the deck). The carfloat is pulled by a tugboat to a railhead in Jersey City, NJ, where the cars are taken off an sent on their way to points west.
4. Only 50% of NYC’s Residential Recyclables are Captured
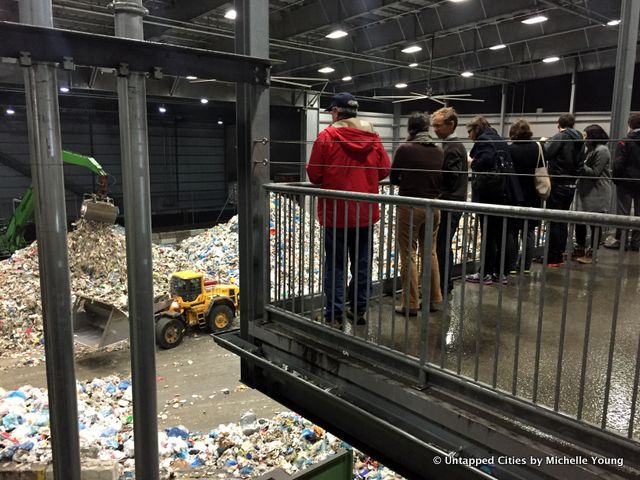
Sims estimates that only 50% of New York City’s residential recyclables are actually captured, meaning New Yorkers are recycling only half of what they could be. Sims is ready to take your stuff, but here’s the full list of what is and is not accepted.
5. 40% of What is Received is Glass, But There is Little Demand for The Material
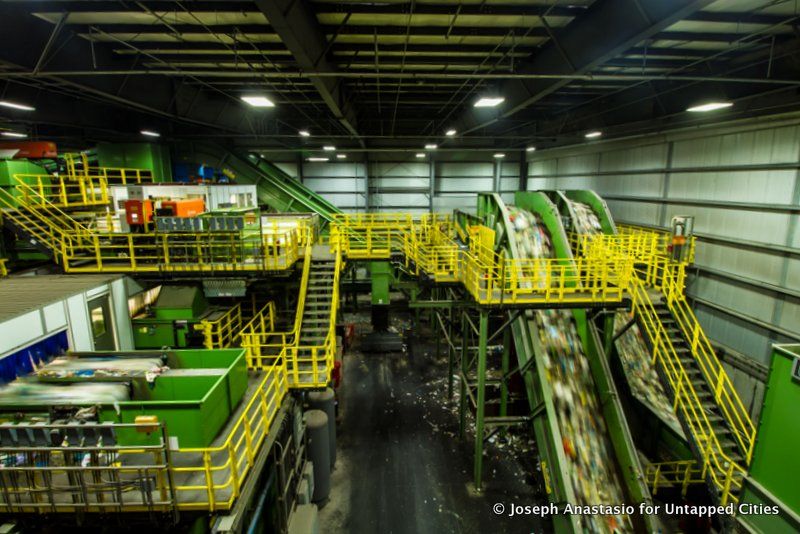
When glass arrives to the facility, much of it is already crushed and in small pieces. This makes the material less valuable than glass that’s picked up whole by manufacturers from grocery stores. In the last few years, there has been a large decline in the number of glass melters in the United States, and “not a lot of companies are investing in glass recycling,” Quinn told us. The glass that is collected goes out to Sims’ Jersey City Recycling Center. Clear glass has more value than colored glass, and gets pulled out of the mix using scanners. Later, some of it will become glass pellets, used below construction roadways like the New Jersey turnpike.
6. The Facility Uses a Combination of People and Technology
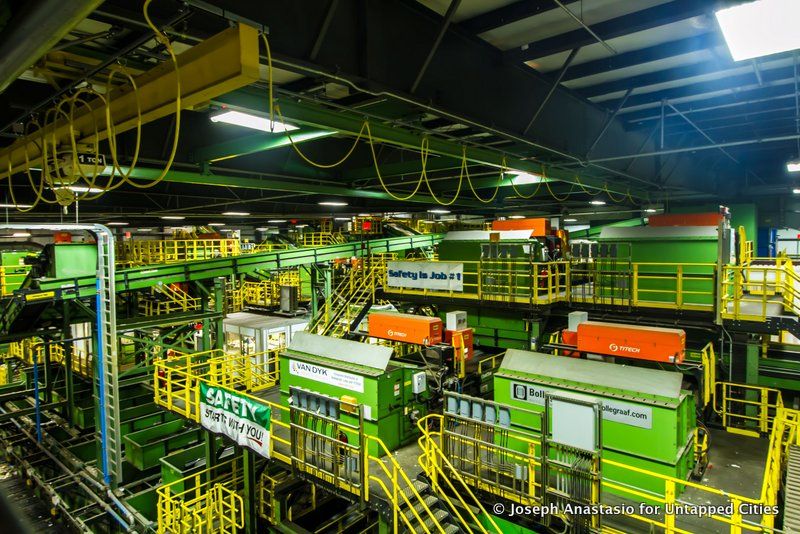
While the priority is always towards more automation, the Sims facility uses a combination of people and technology with 85 full-time employees working here. The facility is open 24 hours a day, 6 days a week with processing occurring 16 hours of those days. The operating equipment processes materials at a speed of a 60 tons per hour. Human sorting is the necessary and last step in the process to identify items that may have been missed in the multi-step automated process.
7. The Many Steps of the Recycling Sorting Process
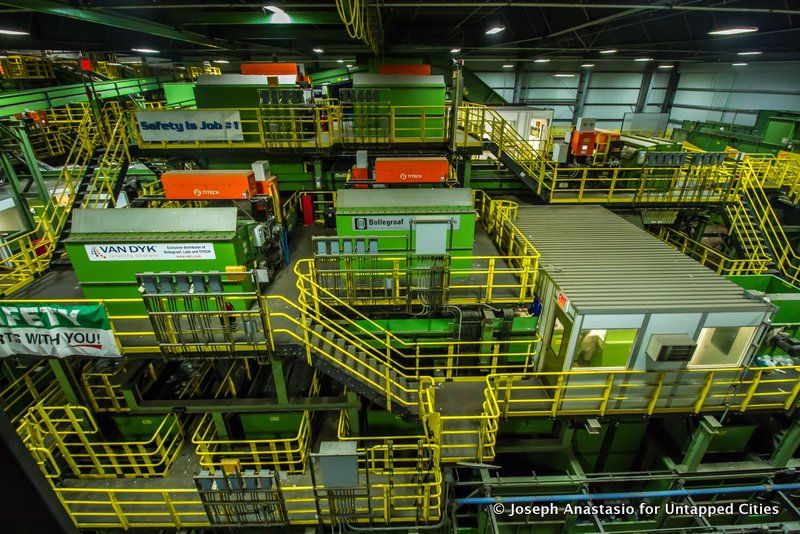
The orange boxes are the optical sorters
After the material goes through the liberator shredder, it goes towards disc screens that jostles the items while pushing them forward. The glass shatters, falls through the cracks and is collected to be sent to the facility in New Jersey. Then, the rest of the items pass over a drum magnet which pulls of all the ferrous metals (metal that contains iron).
Next, the plastics are sorted primarily using the 16 optical sorters (the orange boxes you see in the photographs) which are set to look for particular types of plastics and papers using infrared light. When the type is detected, an air jet is triggered at the end of the belt that shoots the item onto the next conveyor belt.
At this point, most of the plastic, glass and ferrous metal has been removed from the stream, and what’s left passes over an eddy current separator, a reverse magnet that charges metals that aren’t naturally magnetic. Metals like aluminum (the most common material removed using the eddy current), copper, brass, etc. will be repelled. Then, the remaining materials go through a trommel to remove the final unwanted pieces, and the final sort is done by hand.
Each of the separated products are then stored in a large bunker. When those bunkers are full, they will unload onto a conveyor and be sent to the balers. Through a large amount of the force, the balers compress the plastic or aluminum into bales that way about 1,000 pounds each. About 30 to 40 bales can be loaded onto a truck and sent to Sims customers, while other bales leave by rail and barge float.
8. First Large Commercial Wind Turbine in NYC is Here
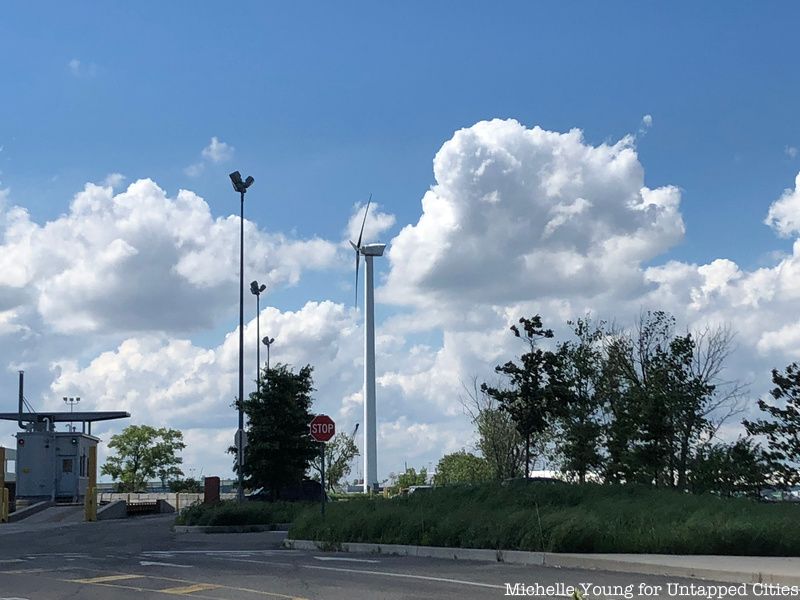
The Sunset Park Material Recovery Facility is partially powered by renewable energy: 5% comes from the 100kw wind turbine, the first large commercial wind turbine in New York City, and 15% comes from solar panels on the building, one of the largest solar power installations in the city.
The facility is a joint project between Sims, DSNY, the Department of Small Business Services (SBS), and the NYCEDC, who have invested more than $110 million in the development of the facility. As requirement of the Request for Proposals (RFP) was that an architectural firm needed to be involved. Selldorf Architects, known for luxury galleries and apartment buildings, won the RFP, creating a building made of prefabricated pieces of almost entirely recycled steel. Selldorf subsequently won the 2010 Award for Excellence in Design from the Public Design Commission.
9. There are Three Artificial Reefs

Photo courtesy NYCEDC
The shoreline in front of the Sunset Park Material Recovery Facility had to be dredged to allow for barge transportation, so to mitigate the effects, the City constructed three artificial reefs to create intertidal habitat for marine and bird life.
10. The Site Was Elevated with Rock from the Second Avenue Subway Construction
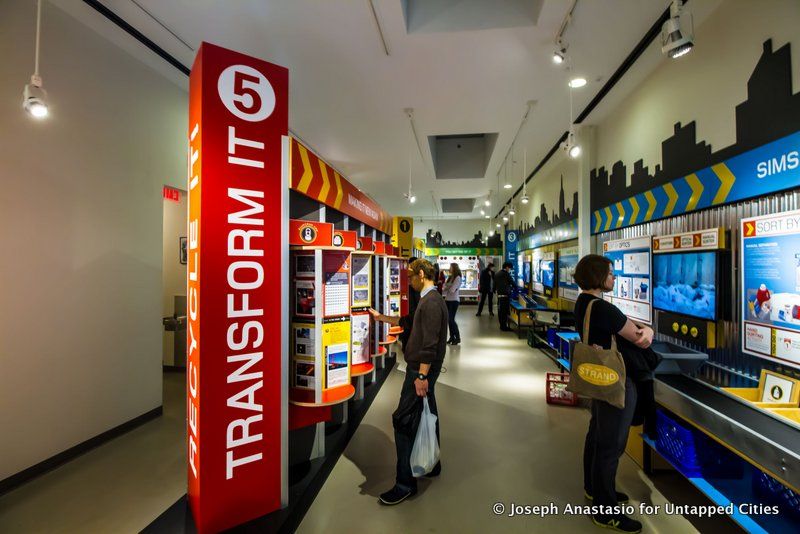
The Recycling Education Center at the Sunset Park Material Recovery Facility
Before Hurricane Sandy, Sims decided to build the facility above the FEMA 100 year flood level requirements, elevating portions of the site by four feet, including all buildings, high voltage electrical gear, scales and recycling equipment. As a result, there was no damage during Hurricane Sandy, apart from non essential equipment that had moved around. The material used to raise the level of the site included both recycled glass and crushed rock from the construction of the Second Avenue subway line. In addition, stormwater is managed on-site, with a gravity-based stormwater system using landscape features, bio-swales and a retention pond.
Join our next Behind the Scenes tours at Untapped Cities.